Digital printing has staked its place in the label and packaging industries, but not all digital technologies are equal. Nessan Cleary offers an overview.
In conventional printing, most of the cost of each job goes into the initial set up with the production of plates or sleeves and readying the press, so that each successive impression becomes cheaper the longer the print run.
The defining characteristic of all true digital print technologies is that each impression costs the same, even though the image may vary from one impression to the next. This means that very short runs can become cost effective, even down to just a few metres or sheets, but as the run lengths go up, so digital quickly becomes prohibitively expensive. However, since each image can vary from one impression to the next, there is the potential to add value through variable data or
versioning to offset the cost, but in general, digital is a short run option.
Toner technology
This is the basic proposition behind the first generation of digital devices, which were based around electrophotography using toner. With electrophotography, a laser writes a latent image to a photoconductor drum. The dry toner particles are negatively charged so that the latent image attracts these particles and this image is then transferred to the substrate. Heat and pressure then melts the toner particles and fuses the image to the substrate. This produces excellent image quality on a wide range of substrates, but its relatively low speed limits it to shorter runs.
Xeikon has been the leading proponent of dry toner presses, having developed a series of web-fed machines with a choice of 330mm widths for the label market and 516mm for packaging, which all offer 1200dpi resolution. The 3000-series presses vary from 9.6 to 19.2m/min, while the faster Cheetah series run at 30m/min.
Liquid toner offers a variation on the electrophotography theme and is the basis behind the HP Indigo presses. Indigo refers to its liquid toner as ElectroInk, and frequently calls it ‘ink’, but it is still an electrophotographic system based on chargeable toner particles. The toner particles are suspended in a fluid, which allows for much smaller toner particles, and therefore higher resolution. In a liquid toner system, the image is formed on the photoconductor drum, then transferred to an intermediate blanket, which is heated so that the liquid evaporates to form the image as a homogenous film, before its transferred to the substrate.
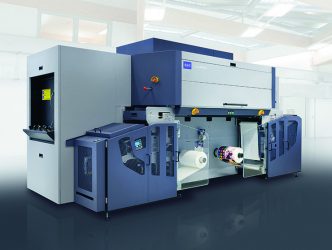
Durst has developed the Tau 330 range of UV inkjet label presses
The presses can all take seven colours, but since each colour must be imaged and transferred to the substrate separately, each colour used slows down the press. Thus in CMYK mode, the HP Indigo 6900 runs at 30m/min. However, each colour counts as a click, so additional colours push up the cost. To this end, Indigo has developed its Enhanced Productivity Mode (EPM), which can reproduce a reasonable colour image from just cyan, magenta and yellow, saving a quarter of the cost per impression, and pushing the speed up to 40m/min. There is also a faster version, the double-engine 8000 model, which can run at 80m/min.
It remains to be seen whether Xeikon or Indigo can squeeze more productivity out of their presses, but electrophotography is a mature technology and is unlikely to push the speed up and the cost down enough to really challenge flexo printing.
Drop-on-demand inkjet
Over the last decade, we have seen the rapid development of inkjet printing, first for labelling and now also increasingly for packaging.
There are a number of different types of inkjet printheads. The most common approach is piezo drop-on-demand. In the typical design, the printhead consists of a row of ink chambers, each with their own nozzle and a piezo electric actuator, made of a material such as PZT laced with piezo crystals. When a voltage is pulsed through the actuator, it changes shape, creating pressure that forces a drop of ink from the ink chamber out through the nozzle. There are several variations on this theme, such as using sound waves to alter the pressure in the ink chamber. The trick is to cut this pressure almost immediately so that some of the ink is drawn back to the nozzle, causing an individual drop to form.
Most labelling inkjet printers currently use UV inks, which will work with a wide range of substrates. These inks are polymer-based, using monomer and oligomer polymers as a carrier and containing photoinitiators, which use exposure to light to kick start a polymerisation process that crosslinks these polymers together. Increasingly vendors are turning to LED arrays to provide the light source, mainly because legislation is outlawing the use of mercury vapour lamps. However, UV LED inks are limited by the photoinitiators available as they require a very narrow UV band to work.
There is an issue that the inks may not fully cure, particularly with LED curing, which limits the use of UV inks for food packaging as the uncured ink can migrate through the substrate. Screen, for example, has addressed this issue with a low migration version of its latest inkjet label press. The Truepress Jet L350UV+LM uses low migration inks that are certified for use with food packaging, combined with a nitrogen purge mechanism to ensure that the inks cure fully.
Ebeam Technologies has also come up with a solution that uses electron beams to cure inks, which does away with the need for photoinitiators. It is working with INX to develop inks and Uteco, which has showed off a small press, the Gaia, targeted at the food and pharmaceutical markets.
Another issue is that UV inks sit on the surface of the substrate and tend to have a high film weight, which leads to dimensional instability with lightweight filmic substrates. Also, UV inks are complex and therefore expensive.
So, for all these reasons most inkjet vendors are working to develop water-based inks to overcome some of the issues with UV inks though for now these are all aimed at the packaging market where the volume justifies the cost. Thus Fujifilm, for example, has developed aqueous ink technology, which relies on a primer to work with a range of substrates and contains a coagulant to limit the risk of dot gain. It uses this approach in the JetPress 750S sheetfed press, which is primarily aimed at the commercial print market though it can print cartonboard.
Fujifilm has also worked with Heidelberg, providing its Samba printheads and Rapic inks for the Primefire 106, which is a sheetfed B1 press, capable of producing 2500 sheet per hour with 1200 x 1200dpi resolution. It is targeted at packaging applications including flexible films and has a seven-colour ink set (CMYK plus orange, green and violet) and is said to be safe for food packaging.
Landa has taken a radically different approach to most other vendors with its Nanographic printing. This also uses a water-based ink, but the ink is jetted first to a moving blanket, which is heated so that most of the water evaporates from the ink effectively transforming it into a hot melt adhesive with coloured pigments. When the warm ink dots are finally transferred to the cold substrate, the sudden change in temperature helps it to bond firmly to the media. Landa says that it will print to many different substrates, including plastic and film as well as paper. The first presses are single-sided devices aimed at the packaging market.
Thermal and continuous inkjet
There are two further inkjet technologies – thermal inkjet and continuous inkjet – which are both suitable for water-based inks. Thermal printheads heat the ink within the ink chamber until it vaporises and creates a bubble within the ink chamber, which in turn forces a drop of ink through the nozzle. The downside of the thermal technology is that the printheads have a fairly short lifespan and are effectively a consumable item.
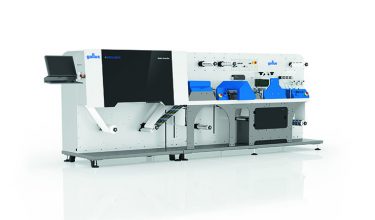
The Gallus Smartfire is a rebadged NS Lion using Memjet printheads.
Memjet has developed single-pass thermal printheads that are widely used by vendors to create entry-level labelling and packaging printers. The company’s original head technology is now branded as VersaPass and is the most commonly used. These heads have five channels so that one head can print CMYKK. They have a print width of 222mm, but can be stitched together for wider print widths. This head produces 1600 x 1600dpi resolution at 9m/min, or 1600 x 800dpi at 18m/min. However, they use Memjet’s water-based dye inks, which limits them to only printing on coated media.
Memjet has now built on this with a new head technology, Duralink, which is faster, with speeds up to 203m/min, and should have a longer life. Each head prints a single colour, but the solution can support up to eight colours. It can achieve resolution of 1600 x 1585dpi at 75m/min. Memjet has also switched to a pigment ink, which should enable it to print to a broader range of substrates.
HP also uses thermal printheads and has iterated the same basic printhead technology to develop a web-fed number of
presses. For now, the company is concentrating on paper-based substrates, such as corrugated packaging, with its C500 presses. This prints to 1.3 x 2.5 metre boards at a speed of 75m/min.
Kodak’s Stream technology is a continuous inkjet or CIJ system. As the name implies, the ink flows continuously through the heads, with heated elements around the nozzles breaking the flow into specific droplets. Most of these droplets are blown off course and recirculated back to the ink system, leaving the heavier droplets to reach the substrate. In theory this approach should be capable of very high speeds. The latest iteration of this is Ultrastream, which was demonstrated as a label press at the last drupa show. This should produce 6.75 picolitre drops resolution up to 600 x 1800dpi at up to 150m/min. It will print to flexible films, but relies on applying a coating to prime the substrate, which can be done either offline or on press. Kodak has partnered with Uteco, which is developing a version of its Sapphire Evo hybrid press with Ultrastream printheads, and which includes an inline coating unit.
In conclusion
Digital printing will inevitably take a larger slice out of both the labelling and packaging markets, but first it will have to become more cost-effective over longer runs. In the labelling sector, this is largely down to higher speeds to increase productivity. For now, one of the fastest label presses is probably the Durst Tau 330 RCS, which uses Samba printheads to deliver 78m/min at 1200dpi resolution, though this is hardly the cheapest label press. For the higher volume packaging market, the holy grail remains water-based inks capable of printing to flexible films without the cost of applying a coating.