BW Converting and Memjet technology hits mainstream packaging, comments Sean Smyth.
PCMC, the Paper Converting Machine Company, is part of Barry Wehmiller Converting Solutions. They are based in Green Bay, Wisconsin, and are currently not the first name that comes to mind when you think of high-volume digital packaging equipment. They want to change this perception and have developed the ION hybrid flexo-inkjet web press. In April they ran an Open House inviting over 100 prospective customers to an event where they showed off the technology.
Barry Wehmiller Group is a 3.8 billion ($4.8 billion) turnover company that also owns Winkler & Dünnebier (W&D), Baldwin Technology, Hudson Sharp who sells pouch making lines and several companies in the tissue and non-woven sectors. W&D is an envelope press manufacturer who is moving into e-commerce packaging equipment, including the W+D 449 E-Commerce machine that has an inkjet option. This scale makes them both a powerful and credible player, they have placed considerable resources behind the development of their new digital press.
The ION press pictured is the development machine in Green Bay. It is a modular hybrid web system that can run flexible packaging and cartons. The configuration is an unwind, flexo pre-print and priming, four-colour inkjet print into additional flexo post-print units, a laminator, dryer and rewinder. Users will specify the modules they require, for flexibles that might include a slitter and turret rewind, with flatbed or rotary die-cutting and sheeting for cartons. A Baldwin camera and control system to monitor quality at full running speed, with corona treatment, web cleaning and various other options as needed. PCMC offers a range of print widths from 813 to 1300mm.
Hitting the market
The first customer is LaCore in Dallas who use the press to print neutraceutical packs that sell through e-commerce channels. Lacore is not a flexible converter company, it is a sales development and investment agency offering vertically integrated business services including product development, testing, merchant processing, state of the art manufacturing, warehousing, and fulfillment operations to support start-up companies. ‘We bought the ION because we could not get the levels of service our brands needed from existing flexible packaging suppliers, so we did it ourselves. The machine was installed last summer and is now working well, producing average runs of 50,000 packs for our vitamins and supplements’, says Jenifer Grace, president of Lacore Enterprises. So not the typical flexible packaging press customer, but an organisation with a need investing in digital flexible technology.
Windell McGill is the launch manager for the ION press. Previously he was with HP and founded the ePac facility in Atlanta. ‘I saw the real opportunities for digital flexible packaging at ePac, and our ION press takes the digital technology to the next level at 400 feet per minute (122m per minute) in widths up to 52 inches (1.3m). This makes it suitable for pouches and mainstream form-fill-seal products, not just for short runs. It offers fast, efficient manufacture. So, it was an easy decision to join PCMC.’ He reports serious interest from both flexible packaging converters and users in North America. The global reach of the Barry Wehmiller Group means they are actively looking for customers in Europe, the company is taking a significant presence at drupa.
Key benefits
Today the press runs at 122m per minute, with an inkjet resolution of 1600dpi across the web and 800dpi in the machine direction. The quality looked pretty good on the flexible jobs they were running to me. Good transition in several skin types, crisp sharp detail and good text, even four-colour text overprint to demonstrate registration accuracy. Reverse out type was clear and legible. There was good saturation with a claimed 70% of the standard Pantone range achievable from four colours on clear PET with a top white reverse print. Having flexo capability means spot colours outside the gamut can be printed, along with metallics and other special effect inks. I couldn’t find any apparent streaks or missing nozzles (and I looked hard), PCMC recommends humidity control in the print engine to avoid any nozzle drying that could affect jetting straightness if the press is left for a prolonged time. The system can employ various techniques to ensure nozzles are kept open and in optimal condition, printing test lines or random background spitting takes place.
After the digital ink is dried there are additional flexo print and coating units, a laminator with drier into a rewind where a Baldwin Defender camera system is placed. This provides 100% defect detection across the full width of the web. This line is 34.5 metres long with a maximum width of 8.5m housing the control systems, inks and the digital front end, a Hyphen Software system feeding a Xitron RIP.
The press uses Memjet printheads in one of the first high volume inkjet flexible packaging systems to reach the market. PCMC bought a company called IPT (Innovative Print Technology) who used Memjet technology on systems in labels and commercial printing and they have scaled up the digital section in combination with transport, flexo print and drying which are PCMC’s core strengths. It uses the Duralink system with pigmented aqueous inks. The demo press has four 22.3cm width heads for each colour, each featuring 70,400 nozzles stitched in an array can be scaled to wider widths. Memjet has other high volume system printing in various applications, several in China.
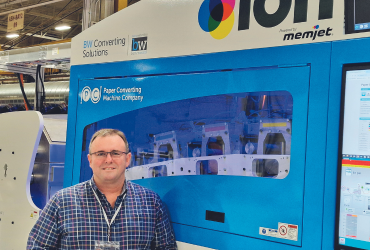
Jason Thelander, CTO of Memjet beside the 4-colour inkjet print module
on the ION press
Jason Thelander is the chief technology officer for Memjet (he’s also an ex-Australian rugby union international – but a very smart and nice guy), he is very happy with the progress on the ION machine. ‘Memjet combines high levels of print quality with high production reliability in our Duralink technology. In the event of a head coming to the end of its life it takes 10 minutes for a replacement to be inserted and the system fully calibrated and back-up running. We are solving the chemstack issues for a rage of flexible packaging substrates. Some require lamination and our ink technology, using patented polymer binders around the dispersed pigment particles, provides the ‘glue’ that enables inkjet to work in high volume flexible packaging.’
Overcoming obstacles
While the costs of the machine and inks were not shared it was interesting to hear that Memjet is used in high volume inkjet applications in China. So, ink costs should not be a barrier when large volumes of ink are being used as will be the case in high volume flexible packaging in the coming years.
At drupa Memjet will be demonstrating a new water-based ink that will not require priming on impermeable films, board and paper including litho coated grades. This will be demonstrated at Hall 5 Booth A25 where I am looking forward to seeing the results. If they can make it work, and they are confident they can, this will be a significant step for the adoption of inkjet into high-quality graphics and mainstream packaging printing. You should also take the time to visit the Paper Converting Machine Co at drupa if you have any interest in digital carton and flexible packaging printing. You won’t be disappointed.
This feature article was first published in the May/June issue of Digital Labels & Packaging, which you can read online here; register here to receive future issues of the magazine