Inspection systems are being used increasingly proactively today to improve print quality and efficiency, writes Sean Smyth.
Back in the day, only a few companies used inspection systems. Press minders looked at reels and screens as the job printed, then reels would be run through a turret inspector for pharma labels, marking defects to be cut out of the job. This reactive monitoring is changing as more production is inspected using high-definition cameras and spectrophotometers as it is printed, looking for a range of defects as they arise. In digital printing, the systems can monitor variable data, and inspect for artefacts such as missing inkjet nozzles, and then initiate corrective action in real time, so waste is not produced. In 2024, the shift is from reactive inspection to proactive monitoring, eliminating the time and cost of faulty production.
There are several providers active in labels and packaging. Baldwin Vision Systems’ print inspection was originally developed for currency, banknote, security and pharmaceutical applications. Today, defect tracking workflows make it possible to eliminate all defects from outgoing products, including labels and packaging, providing perfect quality to brand owners. It is possible to make tactical decisions, fact-based, about which defects do or do not need to be removed, based on customer specifications. This ensures maximum yield and maximum profitability job after job.
Lake Image is celebrating its 30th birthday in 2024. The Buckinghamshire based business supplies a range of inspection systems for security and packaging applications. At Labelexpo in Chicago this year, Lake introduced Discovery PQExpress, positioned as an entry-level print quality inspection system for webs. It features high-performance imaging technology, web viewing capabilities, and automated defect detection.
Esko sells inspection systems developed by AVT: its modular Helios system for labels and packaging. As well as camera systems it also provides densitometer and spectrophotometer tools to provide in-line colour monitoring and measurement. Users set their tolerances for deltaE, providing a simple method of alerting on colour deviation throughout a job. Saving the result means any reprints can be run to the same colour tolerances.
The system can report, meaning an on-press module can report to a rewinder, and the WorkFlow Link automates downstream repair on the finishing machine. The PrintFlow module provides reporting to review job/order/roll reports. On a rewinder, the system automatically inspects 100% of the labels or packs, stopping the rewinder at defect locations to remove sub-standard print before the roll is processed or despatched. At drupa, it featured a new AVT inspection module: the Varnish Inspection Module for labels provides inspection without the need to add UV sensitive pigments or other additives to varnish. Mis-register, partial starvation and full starvation can be detected simultaneously with the existing defect detection, barcode verification, variable data, colour and any other process and quality needs, all in parallel at full production speeds.
Press-integrated
Most new digital presses have vision systems, showing the operator the image with the capability of zooming in to examine areas of print and make adjustments accordingly. Camera inspection systems mounted above the web have been a feature for many years, displaying the result as an aid to the press operator. Images will be digitally controlled and enhanced to show the minder what is happening. Increasingly, these are being linked to the press control to make adjustments on-the-fly in the event of problems. Rather than using colour control strips and registration marks, systems use the artwork file as the master for comparison. The digital twin can include full variable data capability.
Label finishing equipment provider ABG sells fleyeVision, using digital line cameras at resolutions up to 8k to detect print defects such as scratches, hickies and missing text characters, as well as register shift and colour deviations. There is barcode and optical character resolution control, allowing comparison with the job master PDF. Reporting is compatible with ABG Connect, allowing automatic camera set up with live front and back side inspection. The operator can set the acceptable parameters during printing, and there is a warning function via indicator light and alarm, the system able to log the entire production with advance reporting.
At drupa, Durst updated its Hawkeye inspection technology, into Hawk AI, which utilises camera vision systems to automate print quality checking. Hawk AI goes beyond inspection, as it will correct printing errors such as missing nozzles, inline and in real time, with no setup needed and without any operator intervention on the range of new Tau RSCi inkjet label presses.
Bobst is further developing its Accucheck system, which is claimed to make zero-fault labels and packaging a reality. This sophisticated inspection system is integrated into new print and converting equipment to check registration, colour fidelity, and print defects for every label or pack.
Benji Ruhm, chief technology officer at Bobst Mouvent, comments, ‘Bobst Accucheck is far more than a conventional inspection system; it is the only solution in the industry that is fully integrated into the workflow, advancing digitalisation and automation by automating the majority of machine calibrations.’
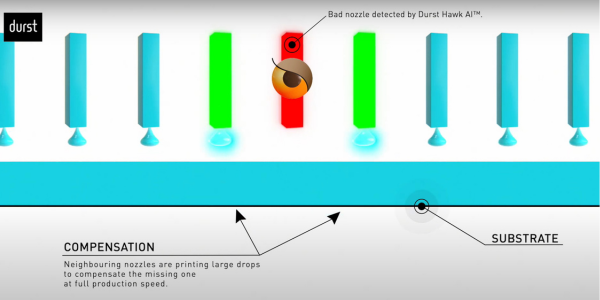
Schematic of Durst Hawk AI automatic nozzle compensation (source: Durst)
At the opening of the new Competence Center in Florence, Bobst demonstrated the advanced capabilities by the operator drawing a line on the labels to simulate a print defect. The mark was captured by the high-res camera and details made available in a production report that could be passed to a rewinder to cut out the affected section, or used to aid manual removal. The inspection system provides production data that can be used to improve performance, as well as automating calibrations to ensure consistent results and simplify the machine operation. These capabilities demonstrate how narrow web production is changing, toward automation and lights-out manufacture.
Pro-active inspection
Increasingly, inspection technology is being used pro-actively to ensure registration and colour consistency throughout a run. Systems identify any print faults and then initiate remedial action automatically in real time on the press and then check the results. Unlike a press minder – even an experienced one – this system can check every impression, linked to adjustments that repair any artefacts or deviations from the pass sheet. For sheetfed systems, faulty product is ejected automatically; in web, areas of concern can be marked and recorded for later removal. The technology will replace many manual quality inspections, pushing the potential for full lights-out automation with links across the supply chain to share real-time information with customers.
Instead of a pass print, the artwork itself will be the master. The digital twin is a virtual version of a job, more than just the artwork. Typically, it incorporates the graphical content of images, linework and text, together with information about the physical attributes, substrate and methods of manufacturing. It may also include production details, run lengths and dates of manufacture along with product information, beyond what is printed on the label or pack. Many brand owners and packaging converters are exploring how they might be usefully used. There are several ways this could happen, to both improve the efficiency of production and adding new functionality to the label or pack, for improved supply chain efficiency or to provide interaction with consumers. The job data in the digital twin will be used to operate and control new presses and finishing systems. Production equipment can generate data that can be used to improve production efficiency, and the inspection system will become the control centre of the press.
As Mr Ruhm says, today’s inspection systems pave the way for future fully automated lights-out production, with guaranteed conformance throughout the job. These are coming soon.
This feature article was first published in the October/November issue of Digital Labels & Packaging, which you can read online here; register here to receive future issues of the magazine