Combining the best of flexo and digital hybrid printing technologies into one production press, doesn’t fit with everyone’s business model, but with recent improvements to the hybrid technology along with a complicated market, is now the time the hybrid press owners can exploit the benefits of this cross-breeds.
What do you identify as? When you introduce yourself are you a digital printer, a label printer, a decorated substrate provider, or for the more extroverted, perhaps High Ink Wizard conjures up the image you wish to portray. There was a time when the UK print sector could be easily divided by preferred print process, and again by the application they chose to specialise in. Today’s market is ultra-competitive, requiring many printers to diversify and expand their product offering. With the traditional sector-lines blurring more and more, is the flexibility offered by hybrid presses becoming more and more relevant to today’s print market?
There’s no sign of the OEMs slowing down on bringing improvements to the existing fleet of hybrid presses on offer today. At last year’s Labelexpo Americas, the Mark Andy launched the DSHD HighSpeed 1200 inkjet/flexo hybrid press is the latest version of Mark Andy’s Digital Series HD line.
Available in 330mm and 430mm web widths the new HighSpeed 1200 model is capable of 146 m/min in up to eight digital colours at 1200dpi, and with the digital engine installed anywhere in the servo-driven flexo platform of Mark Andy’s Performance Series, it offers flexibility of specification both before and after the digital print section, from-roll-to-roll up to full hybrid with decorating and converting inline. In addition, it can run white or invisible security ink at this high speed and single or full colour VDP.
One of the key development decisions made by Mark Andy was to use the two-head system as opposed to native 1200dpi print heads. According to product manager, Ben Luly, ‘Our stainless-steel heads are more robust and reliable with far fewer nozzle outages, making them the preferred choice for labels. We have a better colour gamut, and twice as many grayscale levels as silicon heads, not to mention a higher running speed. If you need consistent performance in manufacturing across many batches, there is only one choice.’
Future Proof
The significant long-term advantage of a hybrid solution is the ‘one pass’ production, which can improve the ROI and total cost of operation/total cost of ownership. Offering flexibility and versatility to produce labels or packaging in either flexo or digital print, or a combination of both technologies.
James Thomas, head of sales and business development at Focus Label Machinery explained, ‘The flexibility of a hybrid press enables businesses to optimise their workflows with the most suitable technology for the task at hand, thereby enhancing efficiency, reducing setup times, and achieving significant cost savings without compromising on the quality of the print, exploring endless creative possibilities by combining different print techniques, colours, and finishes to unveil new avenues for innovation and design.’
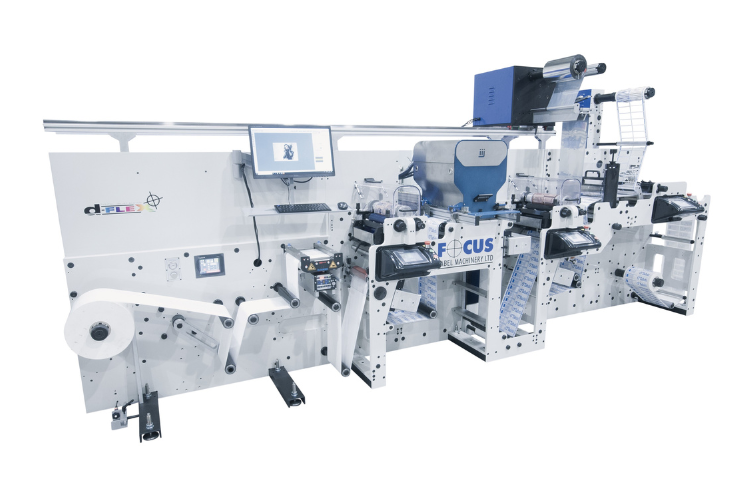
The dFlex SE from Focus Label Machinery
An additional advantage of a hybrid solution is its capacity for variable data printing, personalising printed pieces with unique information, such as names, addresses, or full-colour images by adding variable information, bar codes and sequential numbering, onto generic labels or security labelling and packaging applications.
Mr Thomas concluded, ‘With the printing industry also witnessing a seismic shift from volume production to more customised, flexible solutions, hybrid printing is perfectly placed to support this transition. It offers the best of both worlds: the economic benefits of flexo for large runs and the customisation and agility of digital printing for smaller, more personalised orders. Adding to this a demand for sustainable printing is soaring in today’s environmentally conscious world, so assimilating the benefits of different print technologies is a cost-effective way to slash waste, minimise dependence on potentially harmful materials, and reduce the carbon footprint.’
It’s the one pass possibilities which Bobst is focussed on too. Philip Baldwin, technical sales manager NMW at Bobst UK & Ireland, said, ‘Our commitment extends beyond combining the strengths of digital and conventional printing in a single integrated platform. Our single-source approach means converters can rely on consistent quality and expertise across every aspect of their system.’
The DIGITAL MASTER series from Bobst, available in 340mm and 510mm widths, operates at speeds up to 100m/min with 1200dpi resolution. The modular presses can be configured from a digital-only version to more complex setups incorporating multiple flexo units, embellishment modules and inline finishing. The system uses a single operating system and service interface, rather than combining technologies from multiple vendors.
The modular architecture allows for on-site upgrades as production needs change. Available options include flexo units for primers and spot colours, embellishment features like varnishing and foiling, and automated inline die-cutting capabilities.
Finding the best fit
As with all new ideas or technologies, it takes an amount of time for the industry to adopt and define what is best fit and why. In the early years of hybrid presses, the interpretation of what constituted the best ‘wrap around’ configuration or analogue part of the machine was never really defined. However, hybrid press users are starting to agree on which configurations make the most sense.
Nick Tyrer, managing director, MPS Systems (UK), said ‘In recent times the take up of hybrid technology has accelerated at pace and has centred itself on a streamlined specification that would include a couple of print units before and after the digital engine with cold foiling, a single semi-rotary or full rotary quick change die and a rewind unit, it is felt that this type of set up will cater for 85% of all the work that the printer would want to put through the machine. The reliability of the engines along with resolution and speed advancements have now made the hybrid press a real commercial option.’
However, there is room to spice up your production with some more unusual configurations. Mr Tyrer continued, ‘This is not to say that more exotic configurations are not requested or exist, these however tend to be in the minority and also tend to be product or sector specific. When we start to add screen units and such items as crossover units and turn bars the machine becomes very crowded and less user friendly. Set up times also start to increase and therefore impact on job margin and the number of jobs that can be run per shift thus reducing the commercial proposition of the machine. Our Ultraflex rail system goes some way towards mitigating some of the inflexibility of the rail system by allowing operators to easily configure the rail units in any sequence that is required in a matter of minutes.’
Adding a little extra
Compact print bar units can be fitted above an existing printing and finishing line, transforming existing presses into fully functional hybrid printing machines for a significantly lower cost than a new hybrid printing press. It also allows for additional cost savings from using existing stocks of tools, such as plates and cylinders, and enables space-constrained converters to add new capabilities without expanding their footprint.
Domino offers the N610i-R digital retrofit module which is designed to help converters expand the capability of their traditional presses. Alex Mountis, senior product manager at Domino said, ‘Converters looking to overprint colour labels with monochrome variable data in a single process have the option to add a monochrome print bar, such as the Domino K300 monochrome inkjet printer, to an existing line. The K300 offers high-resolution, 600dpi monochrome of best before dates, batch codes, and 2D codes, as well as label customisation with language variations.